Manufacturing
Empower smart manufacturing, streamline operations, and expand capabilities with our integrated platform.
Streamlining Operations
How Yonyou Addresses
Manufacturing Challenges
Yonyou ERP system tackles these challenges by providing multi-language support, facilitating seamless translation and communication. It integrates Accounts Receivable (AR) and Sales Management modules for real-time tracking of order payments and includes an alert feature for outstanding invoices.
Pain Point
- Lack of Visibility and Control
- Inefficient Production Planning and Scheduling
- High Inventory Costs
- Quality Control Issues
- Supply Chain Disruptions
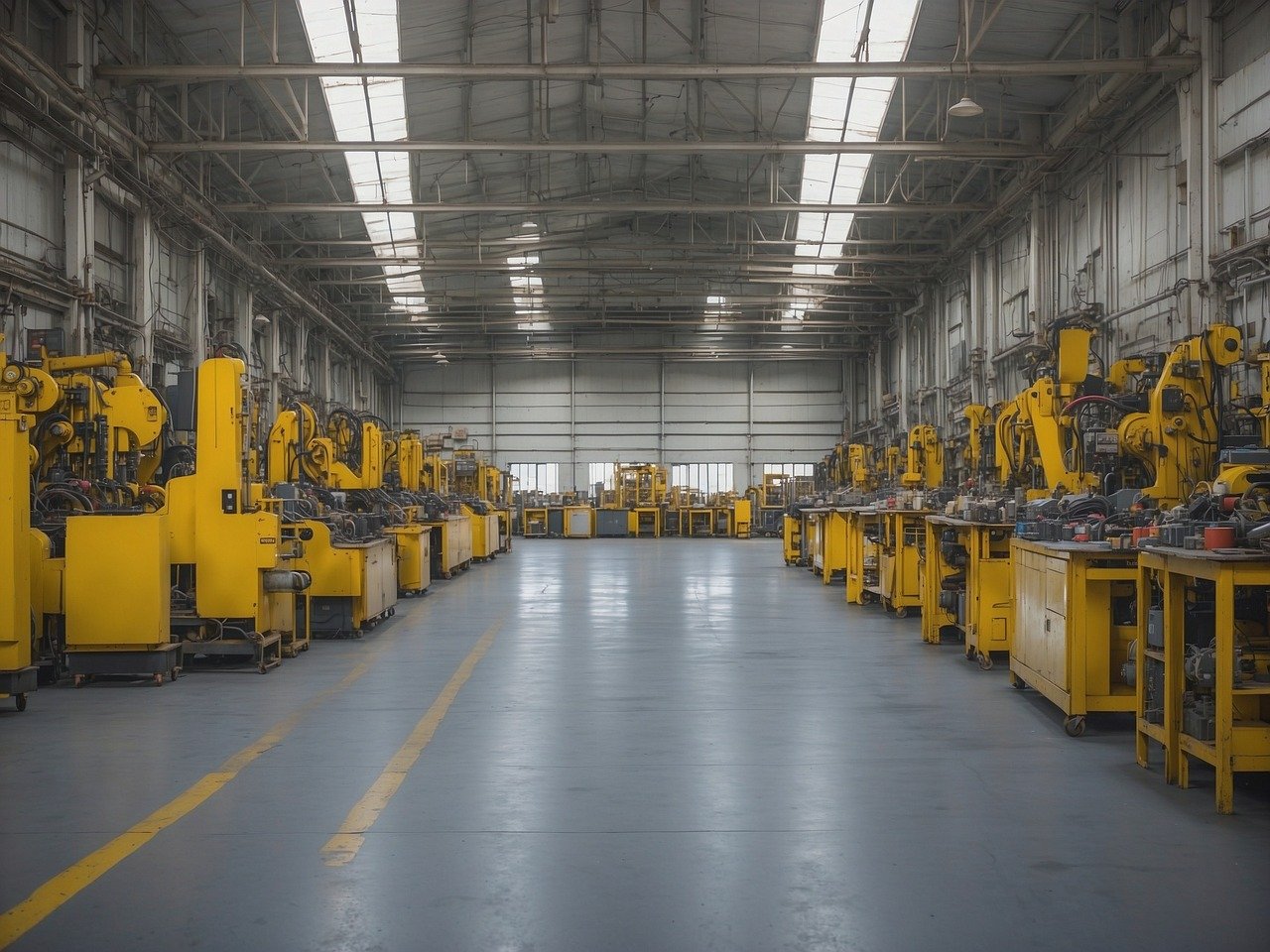
Solution
- Real-time data from Yonyou’s IoT network of connected machines and sensors provides a holistic view of production processes
- Advanced analytics and forecasting tools help optimize production plans, resource allocation, and scheduling, leading to improved efficiency and on-time delivery
Minimize inventory carrying costs and ensure sufficient stock for production
- Integrations with quality management systems and data analysis tools help identify and address quality issues early in the production process
Integration with supplier relationship management (SRM) modules strengthens communication and collaboration with suppliers
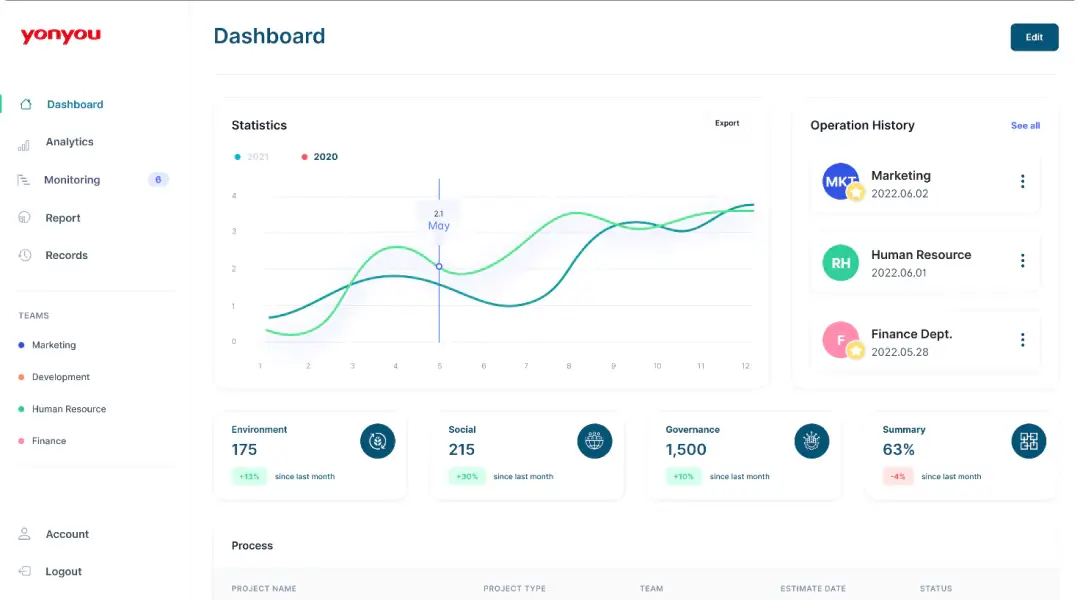
Powerful Benefits
Reduced Costs
Minimizes waste by optimizing material usage and production schedules.
Better Resource Allocation
Ensures your workforce and machines are utilized effectively.
Enhanced On-Time Delivery
Helps you meet customer demand deadlines consistently.
Increased Visibility
Provides a clear picture of your production plan and progress.
Key Areas & Features
Build Your Smart Factory
Smart Factory
- Real-time data visualization from sensors on the factory floor
- Predictive maintenance alerts based on machine data
- Optimizing production schedules based on real-time conditions
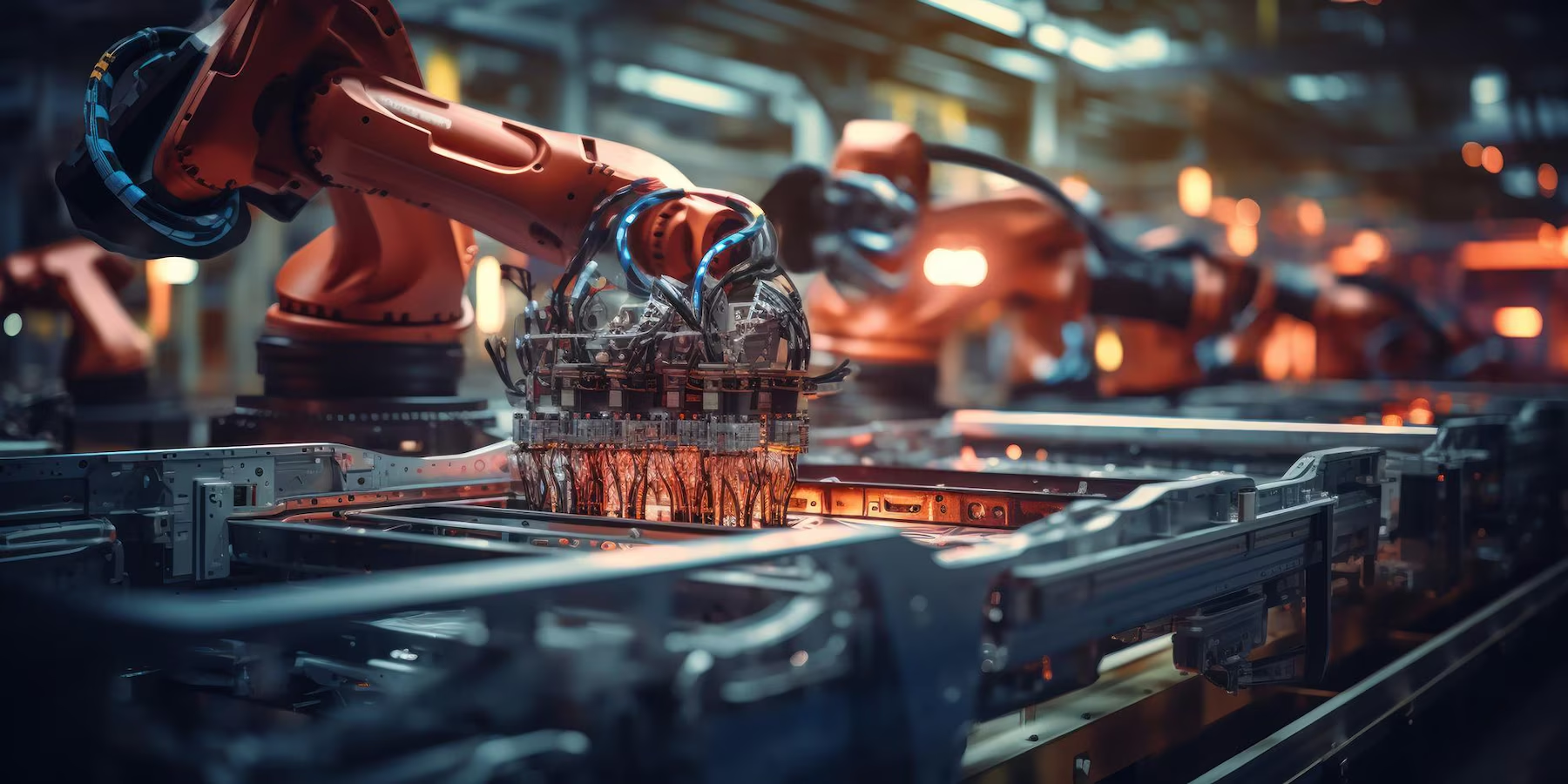
Application Development
- Creating entirely new functionalities within Yonyou’s integrated platform
- Managing an unique production process or an advanced reporting tool tailored to data analysis needs
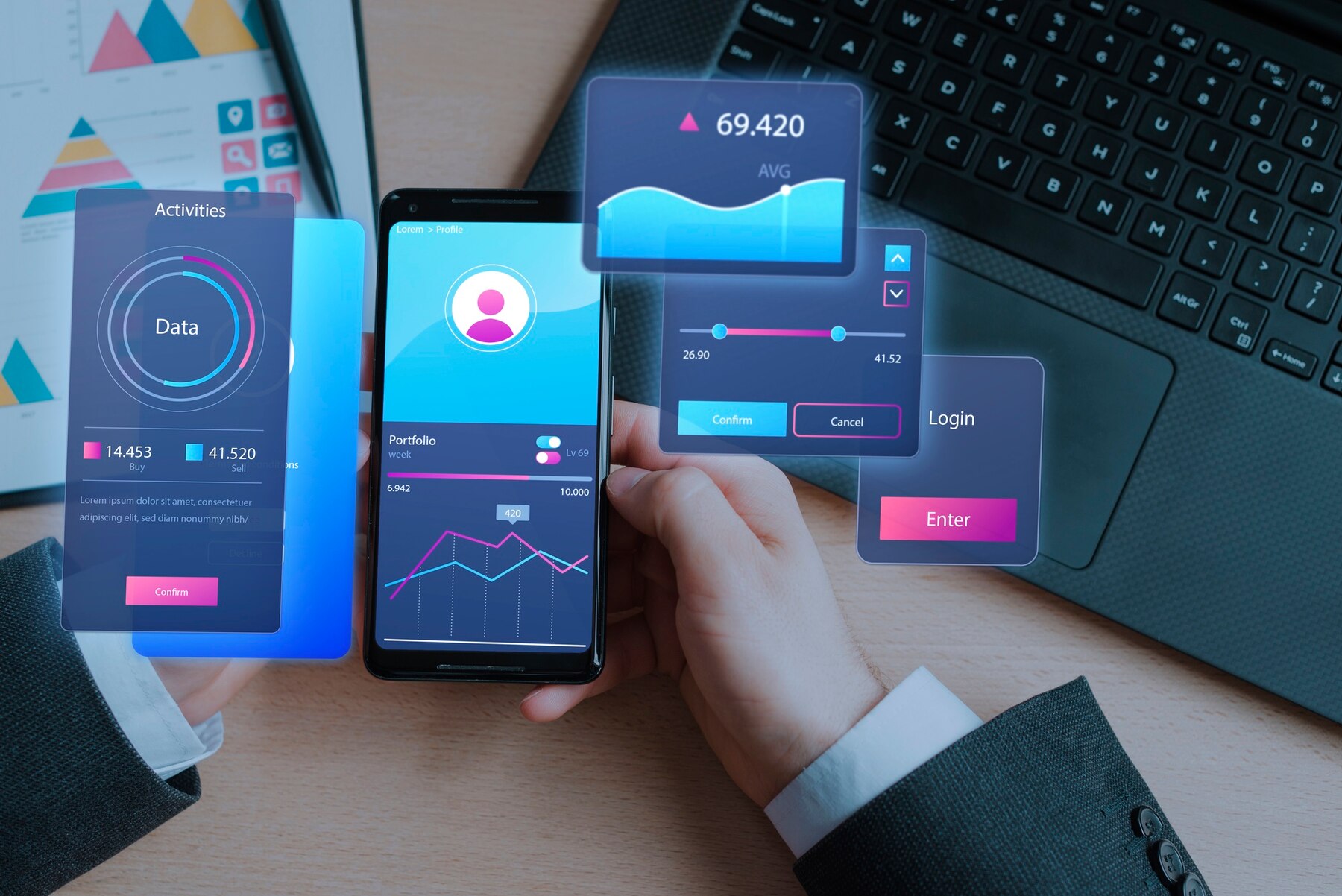
IoT Platform
- Sensors on machines, robots, and provides a more accurate picture of production
- Monitor equipment health, track inventory movement, and even optimize energy consumption based on sensor data
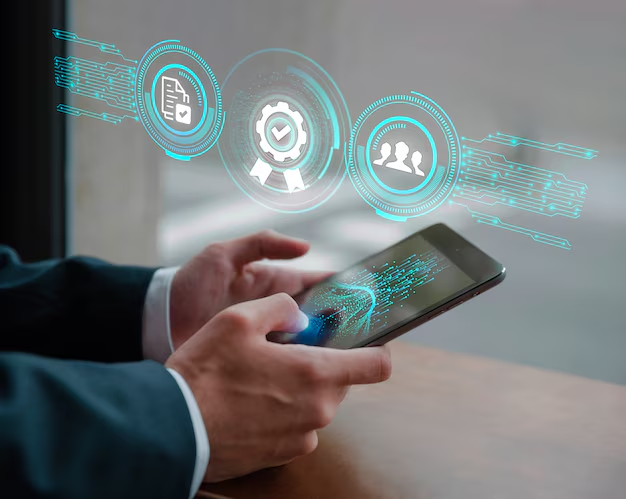
Industrial Brain
- Analyze vast amounts of data from various sources like production lines, machines, and the supply chain
- Identify trends, predict potential problems, and suggest optimizations for production processes
- The ERP can recommend adjustments to production schedules, resource allocation, or even trigger preventive maintenance to avoid downtime
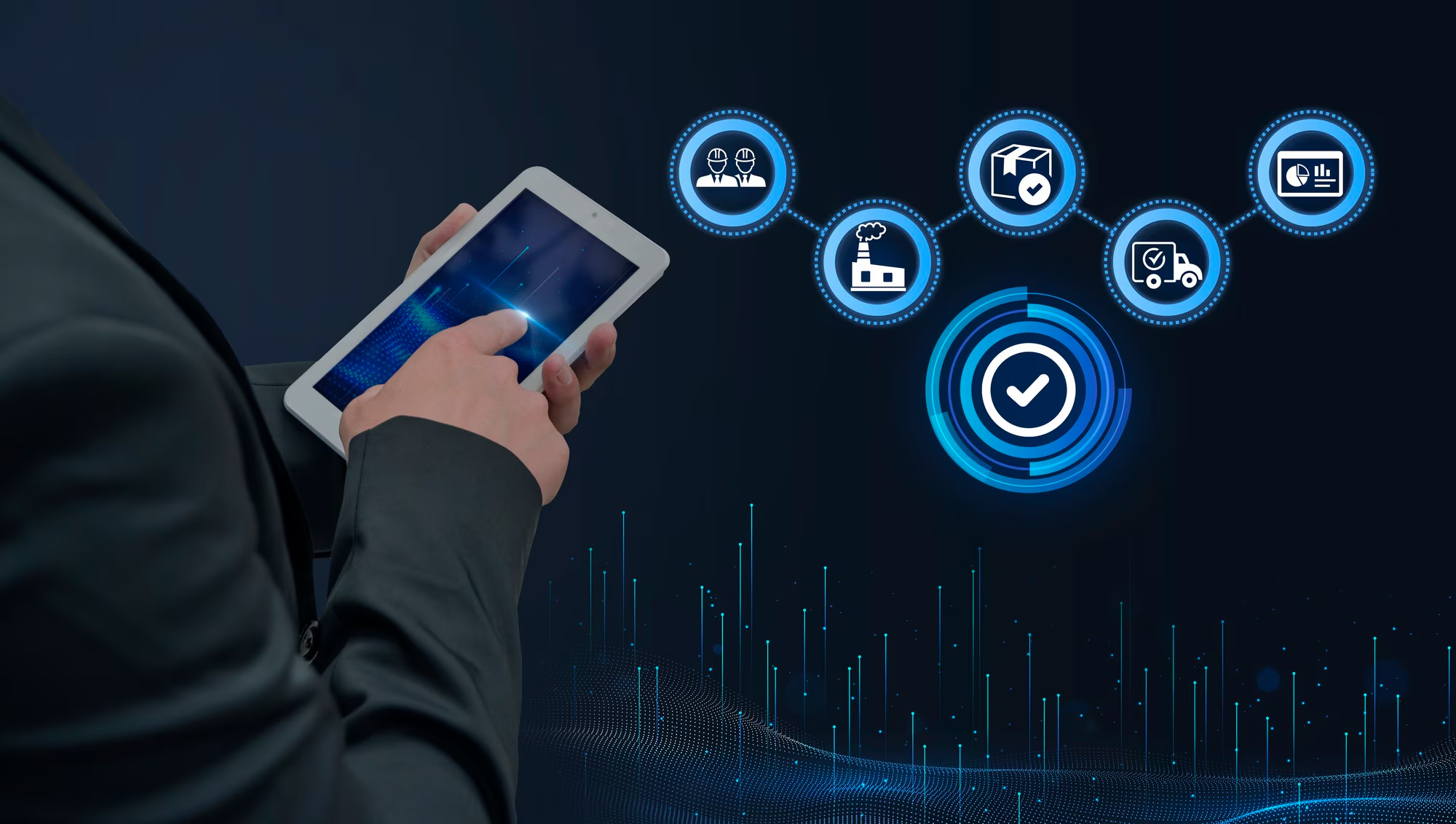
Safe Production
- Help identify potential equipment malfunctions before they cause accidents
- Prevent unsafe operations by halting machinery or alerting workers of potential hazards
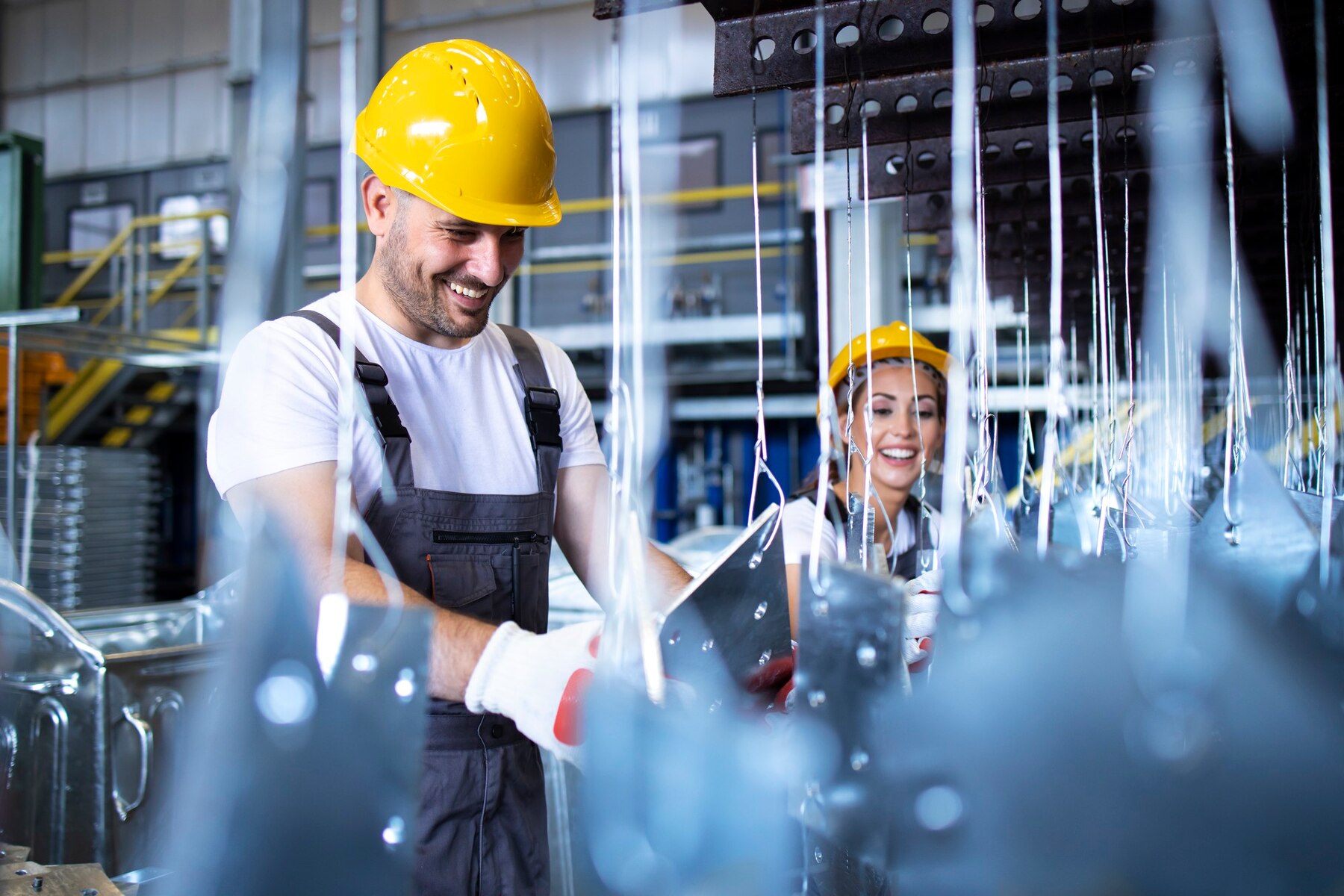
Engineering Change Management
- Initiation and Request Management
- Establish a workflow for reviewing and approving changes
- Identify changes in components and materials (BOM and inventory), update manufacturing processes, evaluate cost implications, and manage document revisions to ensure access to the latest information
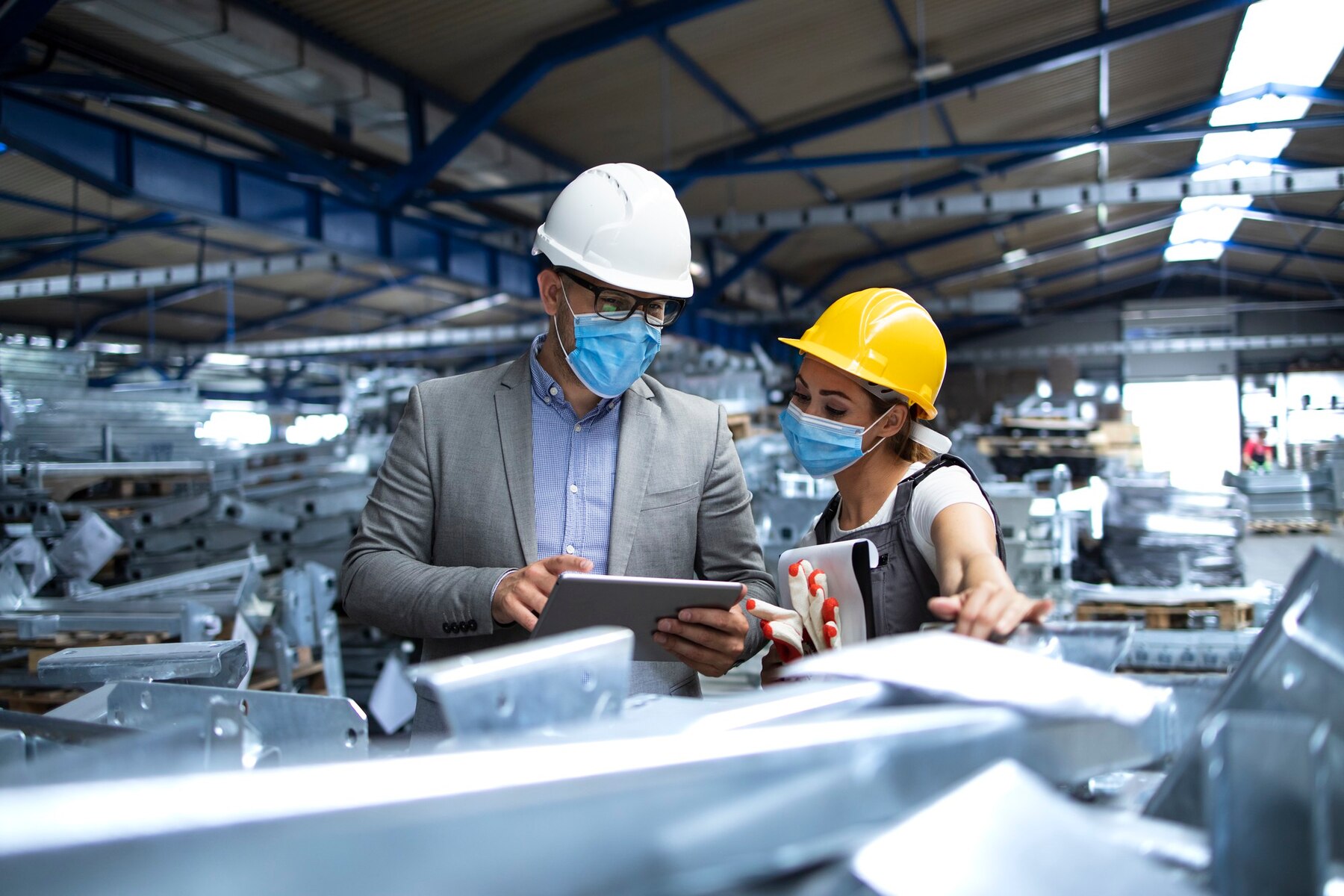
Production Planning
- Anticipated customer demand for your products
- Ensuring to have the necessary raw materials to fulfill production orders
- The time it takes to acquire materials, manufacture products, and deliver them to customers

Production Management
- Encompasses the day-to-day operations of managing production activities, including scheduling work orders, allocating resources, and tracking progress

Shop Floor Management
- Real-time monitoring and control of production activities on the shop floor

Quality Inspection
- Define inspection plans for different products or production stages
- Record instances where products fail to meet quality standards
- Allow recording inspection data electronically, including photos, videos, or sensor readings from automated testing equipment
- Generate reports on inspection trends, defect rates, and identify areas for improvement in the production process
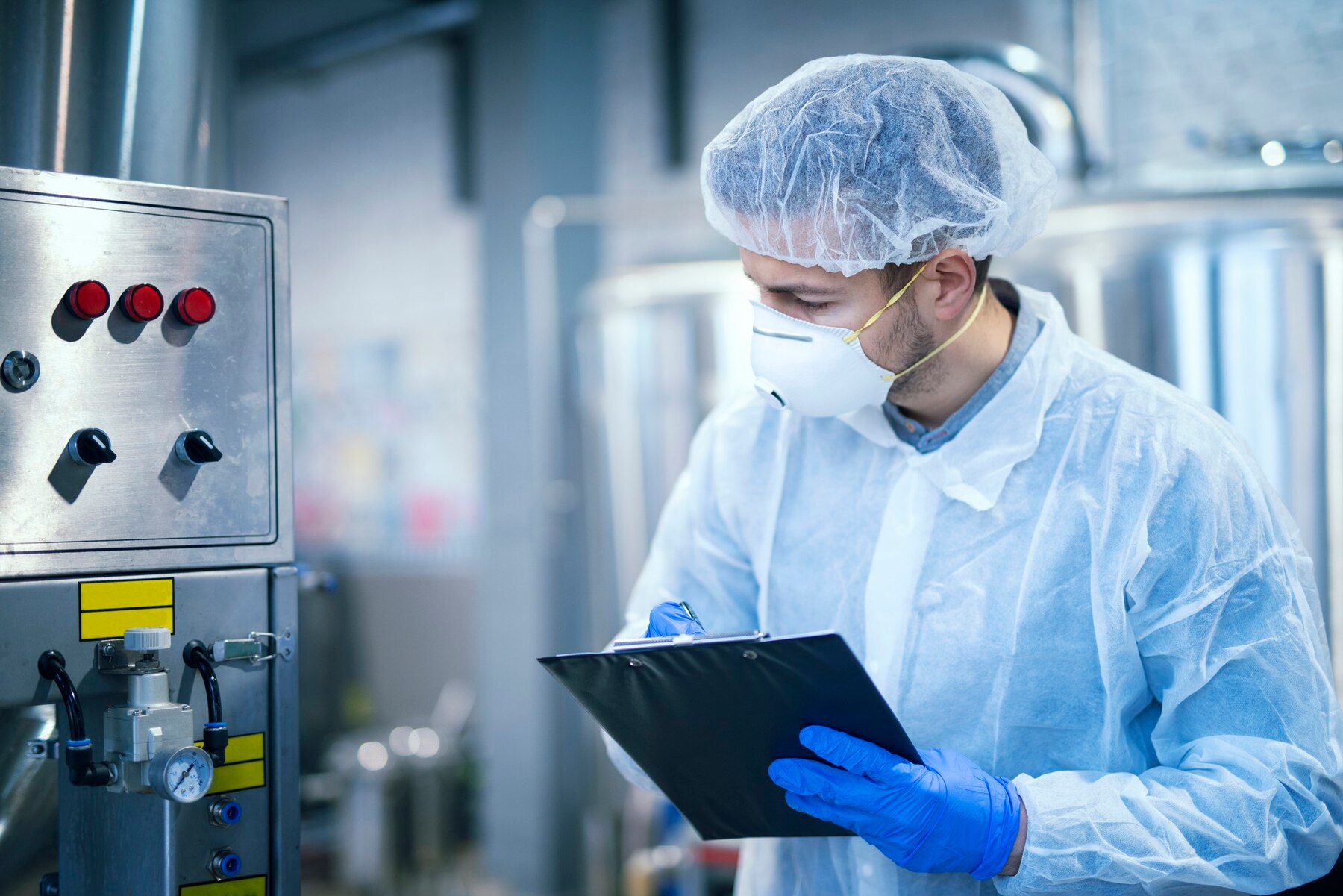
Quality Traceability
- Track individual batches or products through serial numbers
- Store all quality-related documents electronically
- Identify all affected products based on their production lot or serial number
- Facilitate compliance with industry regulations and quality standards by demonstrating a clear audit trail for every product
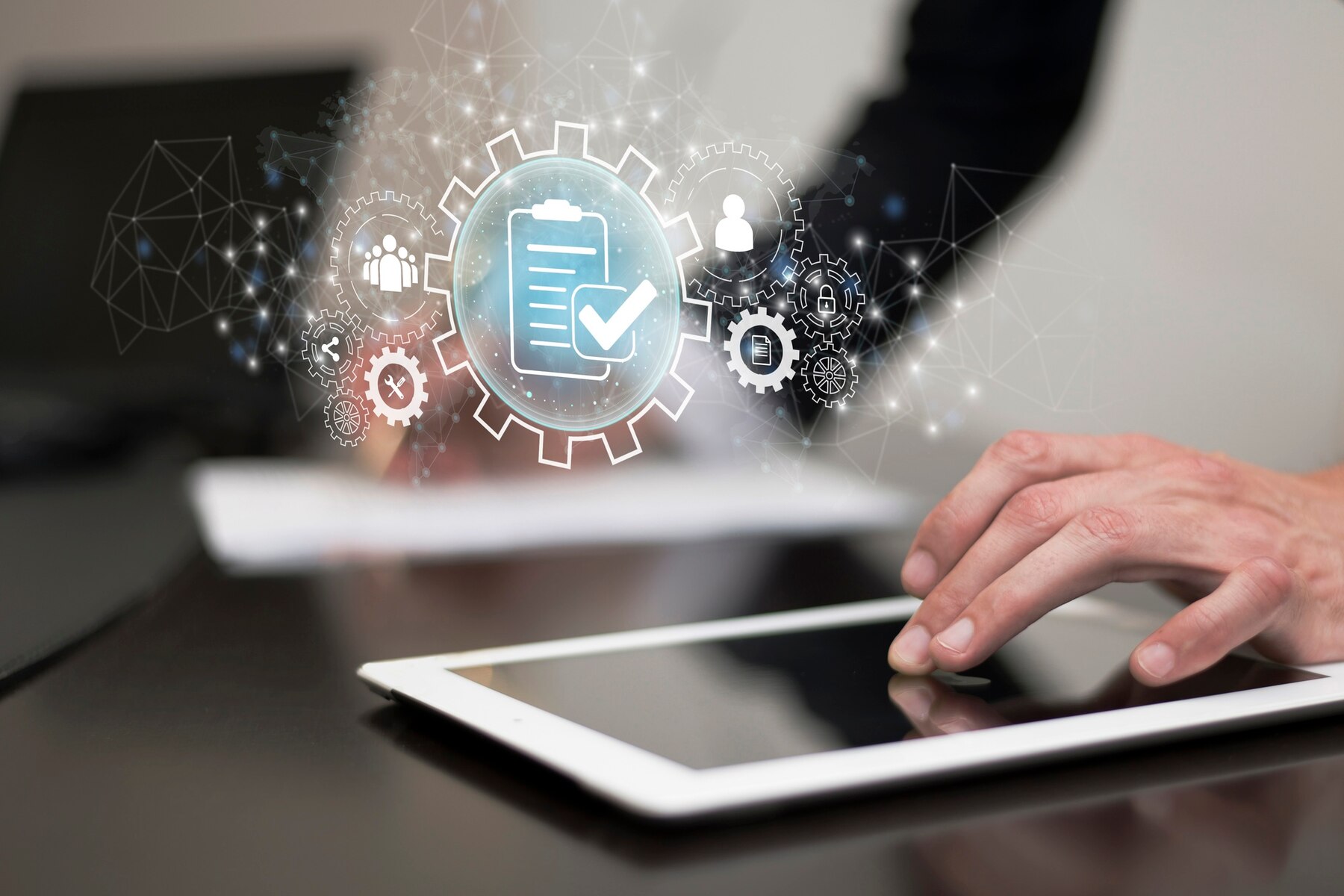
Service Setup
- Create detailed descriptions of the services
- Define the skills and resources required to deliver each service effectively
- Establish pricing models for services with predefined maintenance schedules
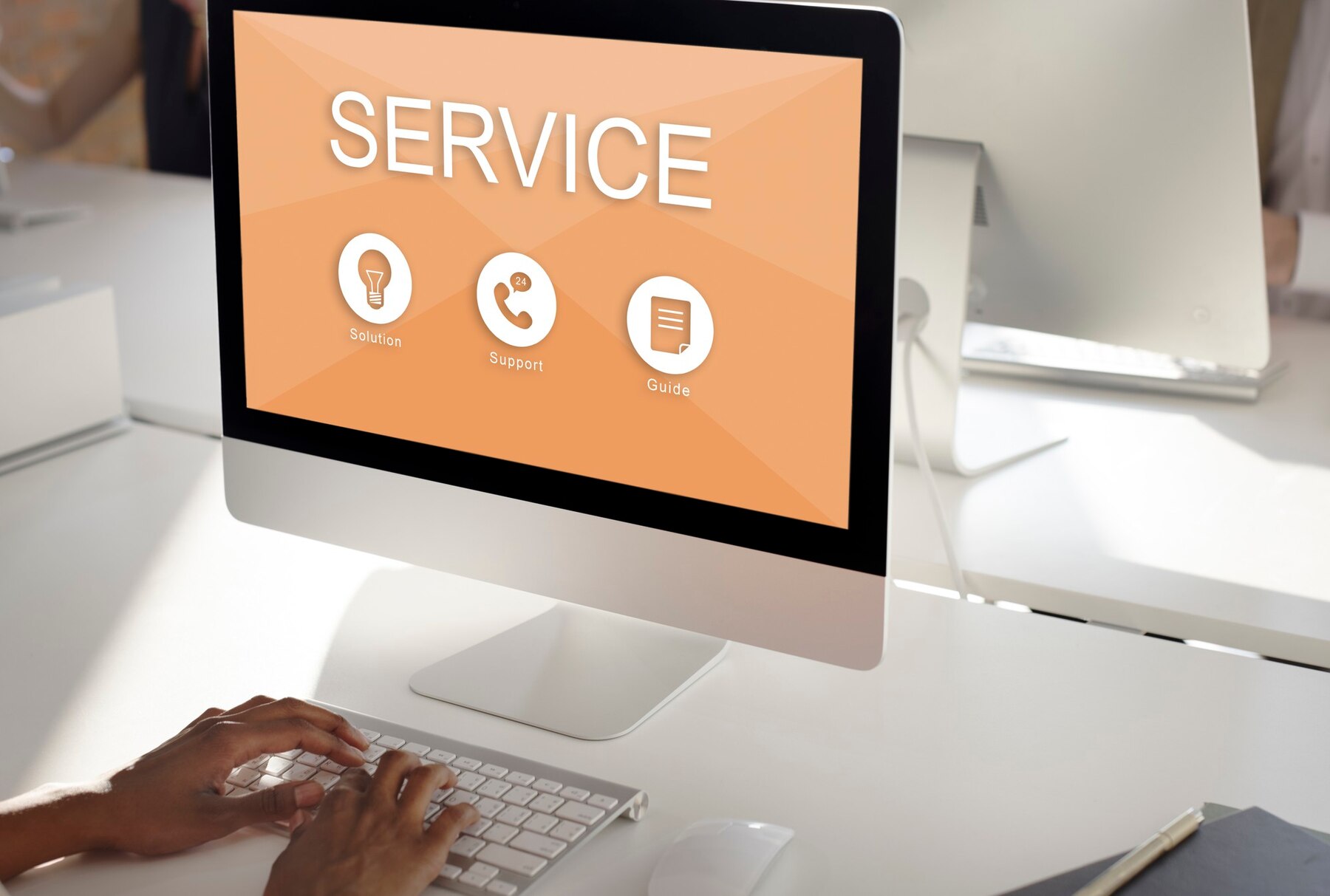
Installation Delivery
- Schedule installation and service appointments based on customer needs, technician availability, and travel times
- Track and monitor the progress of service technicians in the field
- Coordinate the delivery of products or spare parts to the customer’s location and track the delivery process
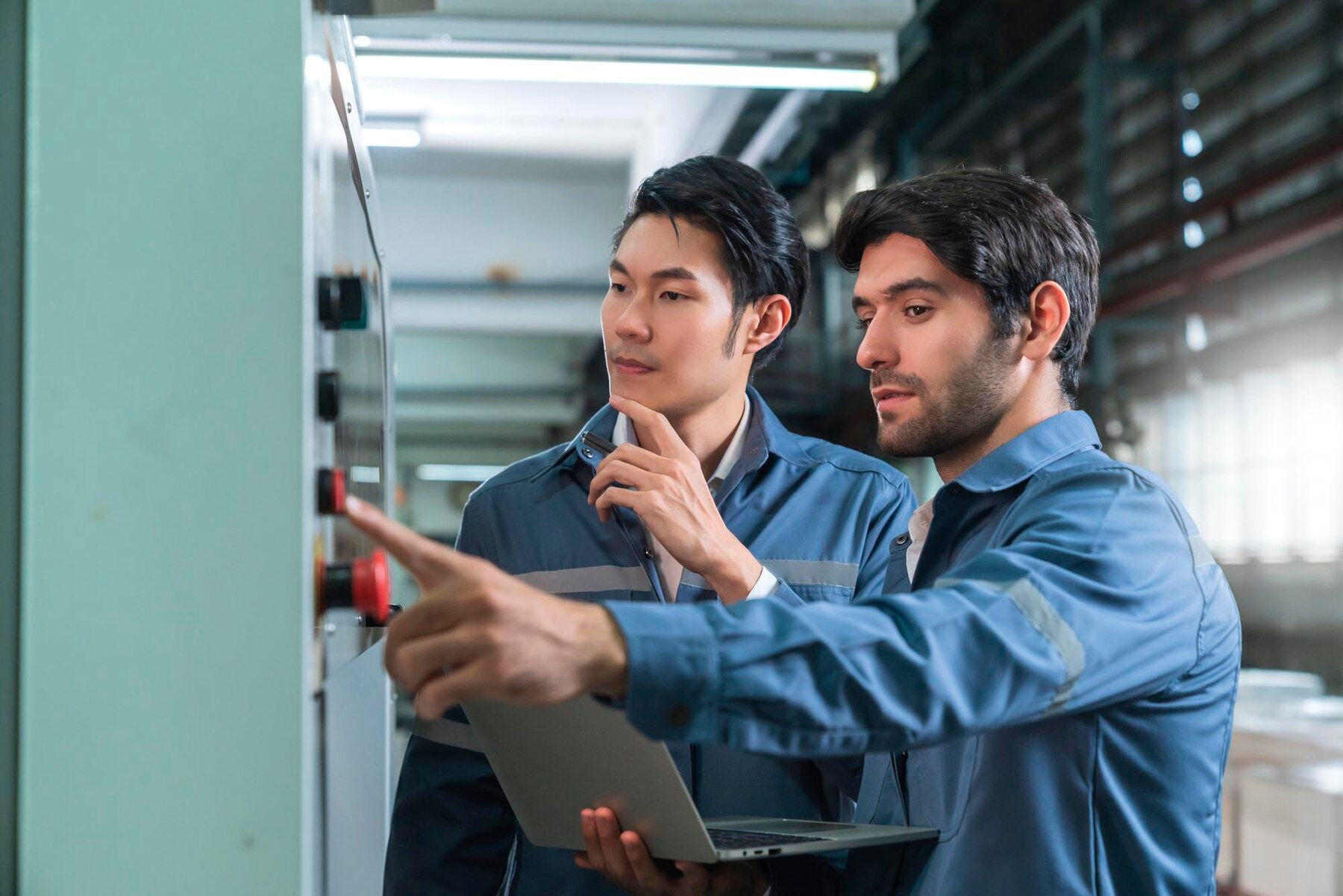
Service Management
- Track warranty periods, manage service contracts, and automate reminders
- Provide a platform for customers to submit service requests, track their status, and receive updates on repairs or maintenance progress
- Capture data from technicians in the field, including work performed, and time spent
- ollect feedback from customers about their service experience
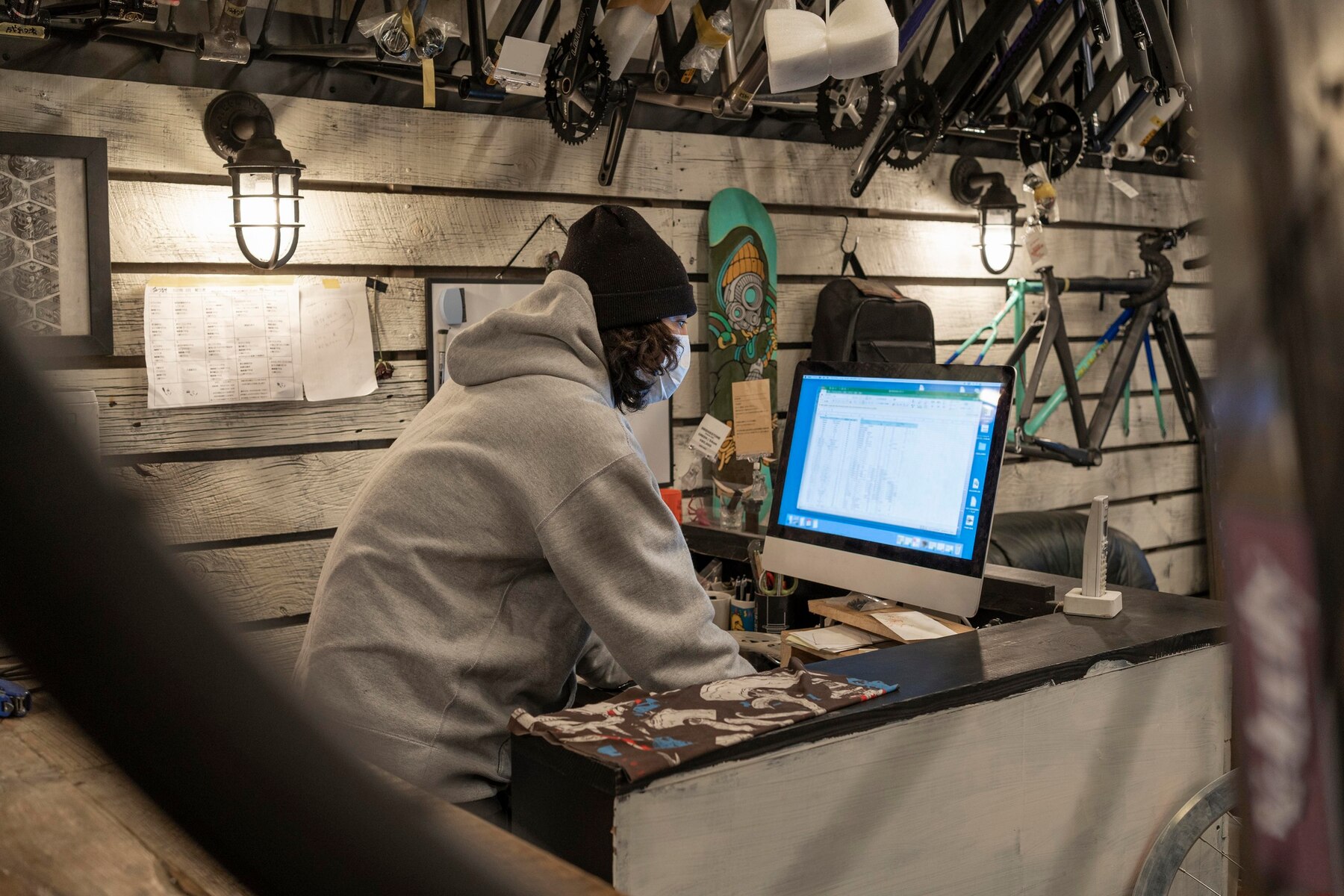
Document Management
- Deals with product data like CAD drawings, specifications, bills of materials (BOMs), and engineering change orders (ECOs)

Centralized Data Repository
- Manages the entire product lifecycle, from initial concept and design through development, manufacturing, service, and disposal
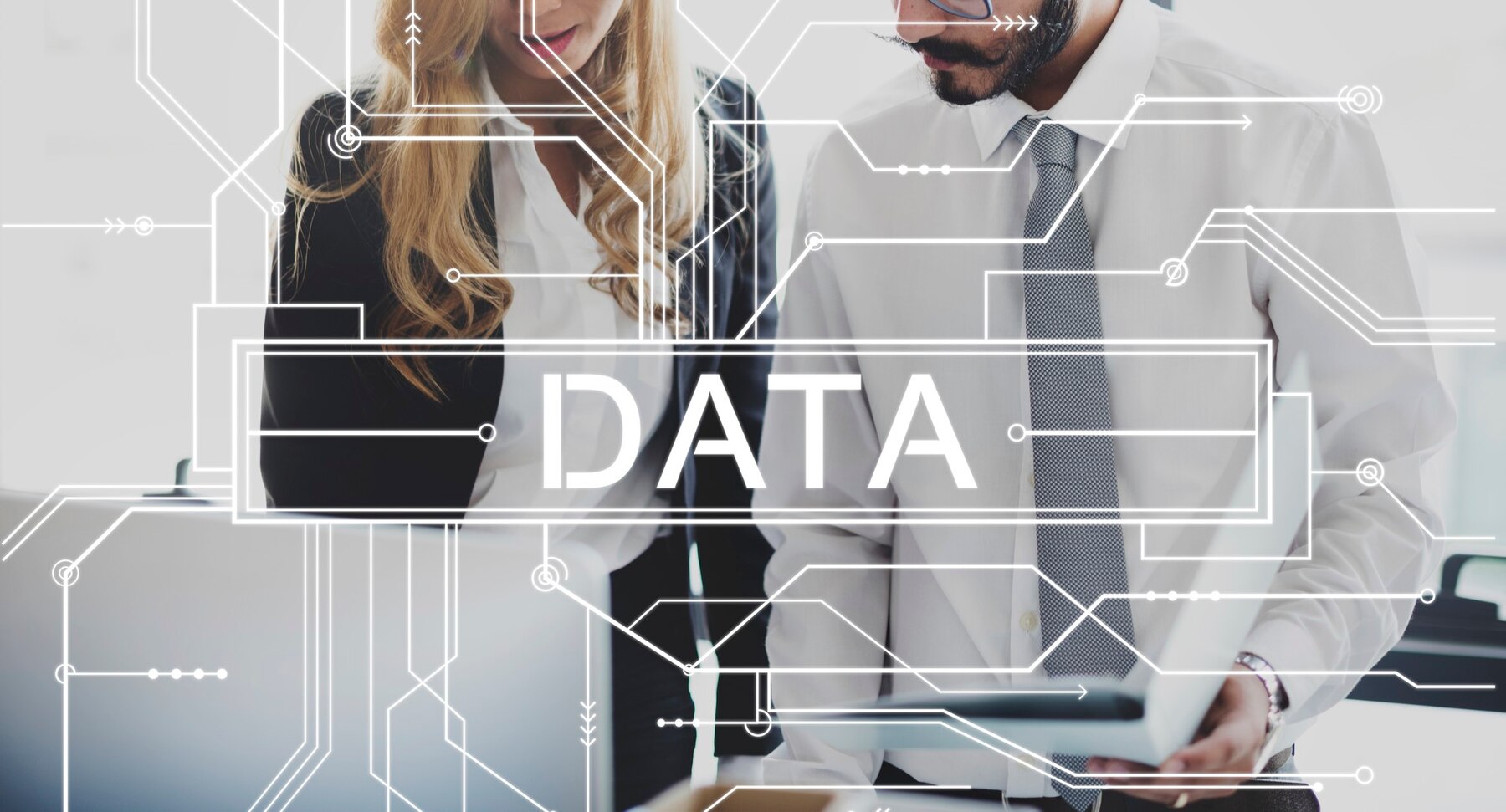
Change Management
- Monitor and document product changes throughout its lifecycle
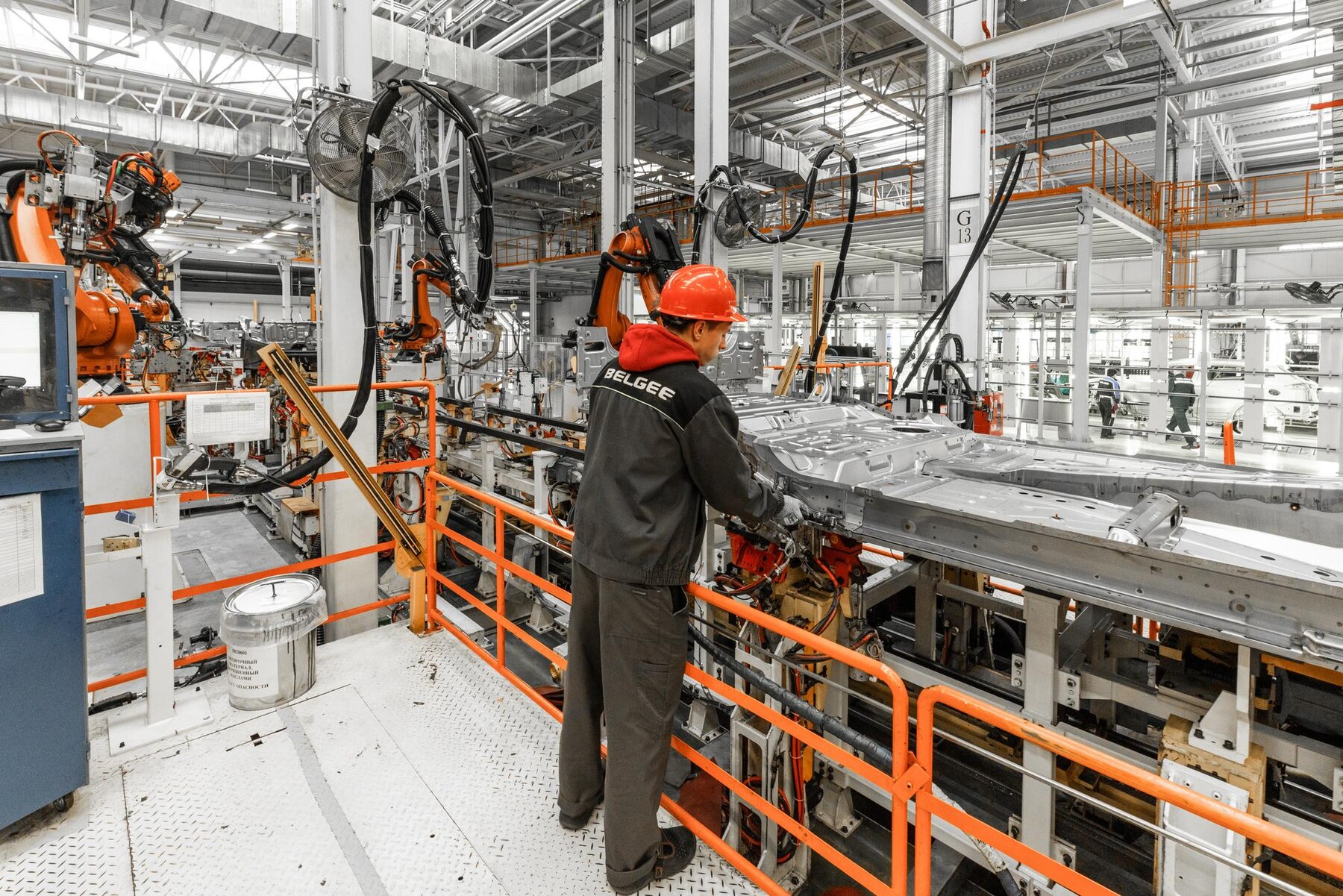
Trusted by 400+ Companies
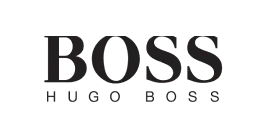
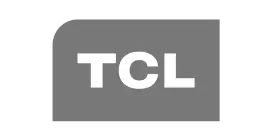
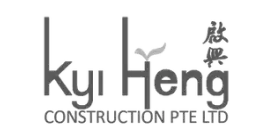
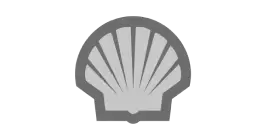
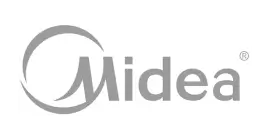
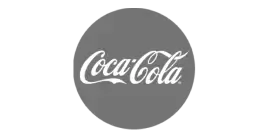
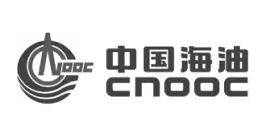
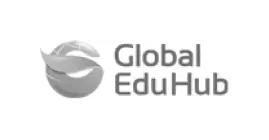
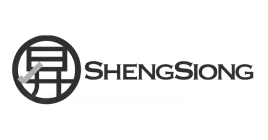
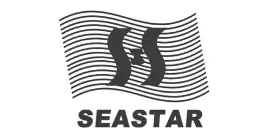
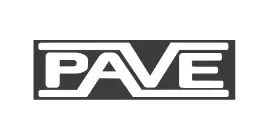
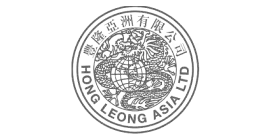
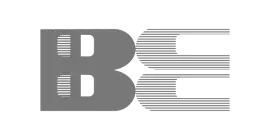
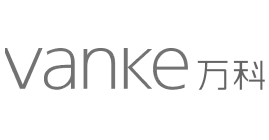
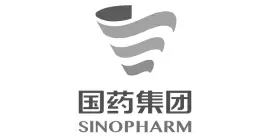
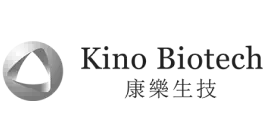
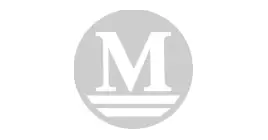
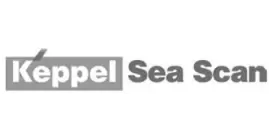
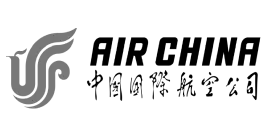
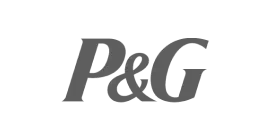
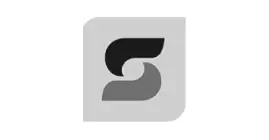
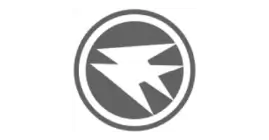
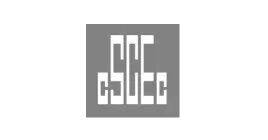
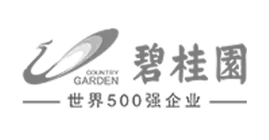
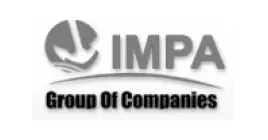
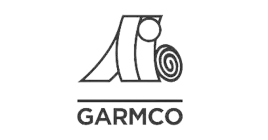
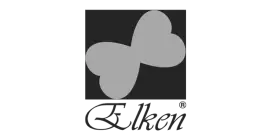
Customer Stories
Success With Our Solutions
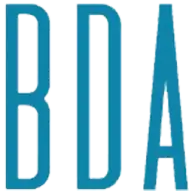
BDA Group
Case Study for Manufacturing Industry
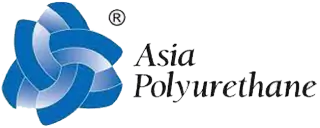
Asia Polyurethane Manufacturing (APU)
Case Study for Manufacturing Industry
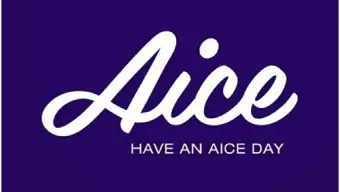
Aice Group Holdings
Case Study for Manufacturing & Wholesale Distribution
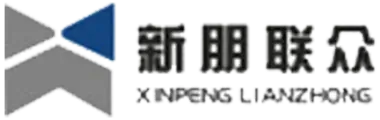
Xinpeng Lianzhong Automotive
Case Study for Manufacturing Industry
Get Ahead With Our Customised ERP Solution and Other Solutions
- 6.5M+ Customers
- 36 Years of Excellence
- 25,000+ Experts
- 6.5M+ Customers
- 36 Years of Excellence
- 25,000+ Experts